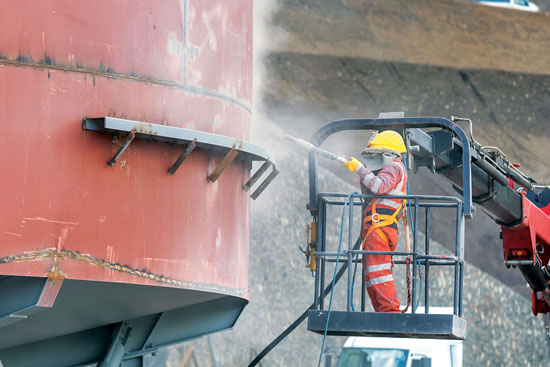
Steel Sandblasting
As Ardam Group, we also carry out steel sandblasting according to your sector and usage area.
What is Sandblasting and Painting?
- Steel oxidizes over time when it comes into contact with oxygen. Rain water, sea water and some acids accelerate this oxidation even more. We simply call it rusting. However, rusting is not an issue to be taken lightly. Rust breaks the resistance of the steel and causes it to rot. When every object made of iron and steel rots, it becomes unusable after a while and ends up as a junkyard.
For this purpose, we must prevent the contact of the material with oxygen in order to be able to use the material we have for years. There are some ways for this.
- The material must be plated with Chromium (This is a very expensive method and can only be done in small parts.)
- The material must be painted. (It is the simplest and most economical method applied all over the world today.)
Sandblasting Materials:
- Silica: Silica sand, which has very fine varieties, is generally used when sanding with light intensity on thin sheets.
- Basalt: This sand, which can be said to be less dusty, is generally used in indoor environments where the sand can be recycled.
- Grit: It is the type of sand with the least dusting and the best sandblasting power. It is actually iron rot, not sand.
Sandblasting Types:
- Automatic Sandblasting: Generally, the sandblasting of steel construction elements that have not been cut or welded work yet, or steel materials that have been welded to a certain extent, are sandblasted in automatic machines. The advantage of this system is that the material large enough to enter the machine can be blasted quickly and economically. The disadvantage is that large materials cannot be blasted. For example, you cannot blast a machine, a fuel tank, a container, a steel bridge, or any other large material that needs to be blasted in place with a blaster.
- Manual Sandblasting: Portable sandblasting consists of a compressor that produces high pressure air, a sandblaster, hoses, etc. It can be done anywhere with hardware and can be applied to all kinds of materials and generally large materials. However, the disadvantage of this method is dust formation. In fact, it is possible to blast without dust, that is, without dust. Wet blasting is used to blast without dust. In this system, when blasting is done, wet sand is sprayed on the blasted material with a special method, so dust does not come out. Wet blasting is mostly done in marinas, on the boatyards, on fiber or wooden boats. The aim here is to sandblast the boat without disturbing the environment with dust. In addition, wet sandblasting is preferred when plaster removal - scraping, wall cleaning (paint scraping - removal) will be done by sandblasting on marble or similar natural stone surfaces by sandblasting method in construction or buildings in the city. Wet blasting can also be done on steel surfaces, but paint should be applied to the surface immediately after the blasted area. Since this paint is a special paint, its cost is high. For this reason, wet blasting is not preferred on steel surfaces.
Sandblasting and Painting Areas
- Steel Constructions
- Ship, Yacht, Boat Surfaces
- Business Machines
- Truck – Trailer Trailers, Tankers, Dekovil, Vacuum Truck, Trans Mixer
- Fuel, Detergent, Acid Storage Tanks
- LPG Tanks And Cylinders
- Cargo Containers, Garbage Containers, Drums and Barrels
- Electric panels
- Water Tanks
- Electric Motors And Generators
- Transformer Silica Sheets And Bodies
- Constructions
- Making Slippery Floors Non-Slip by Sanding
- Historical monuments
- Cleaning of All Kinds of Surfaces and Floors in Industrial Facilities